研磨振动研磨抛光机已经在企业的表面抛光处理中普遍运用,但是如何让振动研磨抛光机发挥它最好的抛光效果,让工件抛得更好并且能更好地节约抛光材料,这是对企业的表面抛光来说是一个十分重要的问题,研磨振动抛光机对各种工艺品的去毛刺、抛光效果有着非凡的效果,经过该机抛光后的工艺品,晶莹剔透,光滑透亮。今天我们来谈谈关于如何更好更正确地使用振动研磨抛光机,让您的企业更节省成本和开支。
振动抛光机采用高频率振动,使工件与抛光磨料、研磨液等密切均匀混合,机器在工作时工件与抛光磨料随着机器的运转,呈螺旋涡流状滚动,从而达到对工件抛光的效果。本机适合于研磨切削或抛光工作物表面的毛刺,飞边,氧化层等。尤其是那些外形复杂,孔内死角的工件使用该抛光机抛磨能得到较为理想的效果。经过无数次的反复试验,对金属类工件,在前道加工过程中所留下的毛刺、飞边等经过振动抛光机抛磨后会产生意想不到的效果,通好大大提高生产效率,与传统的抛光方式相比,大量减少人工的投入。但是如果你的工件上有特大的角边和特大的焊接疤痕,那么如果用振动研磨抛光机来处理的话会化掉很大的抛光磨料和时间,所以如果碰到这样的情况建议您先作机械的粗加工后再进行研磨抛磨。
为了将振动研磨抛光机的抛光效率达到最佳,抛磨出来的工件效果最好,振动研磨抛光机去毛刺过程最好进行粗抛和精抛两道工序,这样既节约时间和原材料,又能让工件表面更好。
振动研磨抛光机在抛磨时一定要加入适量研磨液以增强研磨效果,是因为研磨液既保护了工件与工件间的碰撞又增强了抛光磨料对工件上毛刺的切削。
我们在对工件进行粗抛和精抛两道工序时,必须要选择好每道工序所用的抛光磨料,这是关系到处理出来的工件的表面光滑效果的关键所在,对这两道工序抛磨时我们建议使用刚玉类抛光磨料,因为刚玉类抛光磨料对工件的毛刺、飞边的切削效果更明显。待工件的毛刺和飞边去除后,必须更换抛光磨料对工件表面再进行一次美化,即对工件进行最后一道工序的抛磨(表面光亮处理)。表面光亮处理时不提倡使用刚玉类抛光磨料,表面光亮处理必须选择对工件表面更具光亮效果的磨料,具体应因工件材质而定。振动研磨抛光机在表面光亮处理过程中一定要加入适量的光亮剂,才能使工件经过处理后发挥尽善尽美的效果。
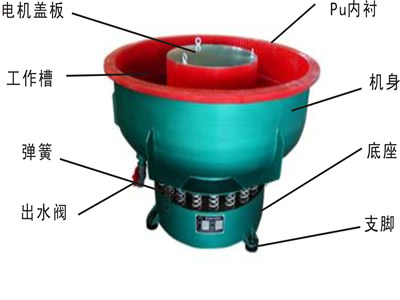
在进行抛光前先将工件和抛光磨料放入振动研磨抛光机工作槽内,工件和磨料放入时要尽量将其在振动研磨抛光机工作槽内放均匀,再加入适量清水后启动机器,待机器将工件和抛光磨料混合均匀并湿润后停机,打开放水阀将机器工作槽中的多余的水排出,防止放入研磨液后泡沫四溅影响操作。接下来再放入研磨液,研磨液的投放量以工件重量的5%左右为宜,放好研磨液后开启电源研磨抛光机正式开始研磨。待振动研磨抛光机工作几分钟后,因为抛光磨料在工作中需吸收一部分水分,所以视工作槽内工件情况可适量加入少许清水。振动研磨抛光机在抛光过程中可随时抽查工件的抛光进度,其抛光时间以工件上毛刺和粗糙度来决定抛光时间的长短。待工件达到光整效果后打开出水阀,用清水将工件和抛光磨料冲洗干净。为了使工件表面的光滑度更理想,一般在去除毛刺过程中进行粗抛和精抛两次抛磨。
工件经过粗抛和精抛后工件表面虽然毛刺已去除,但表面呈白色并无光亮的感觉,要得到工件光亮的表面,必须使用光亮剂再次抛磨。光亮剂的投放量为工件重量的2%左右,选好抛光磨料并与工件一起放入振动研磨机工作槽内,开启振动研磨抛光机电源,抛磨至工件光亮后出料,经防锈液处理即为整道抛光工序完成。
抛光工件效果图
|